HPMC LK500 for Self Leveling Mortar
Product Description
Hydroxypropyl Methyl Cellulose Ether LK500 is an additive for mortars that require high fluidity. Its main function is to increase its water retention capacity and suspension capacity in the mortar and has little effect on fluidity.
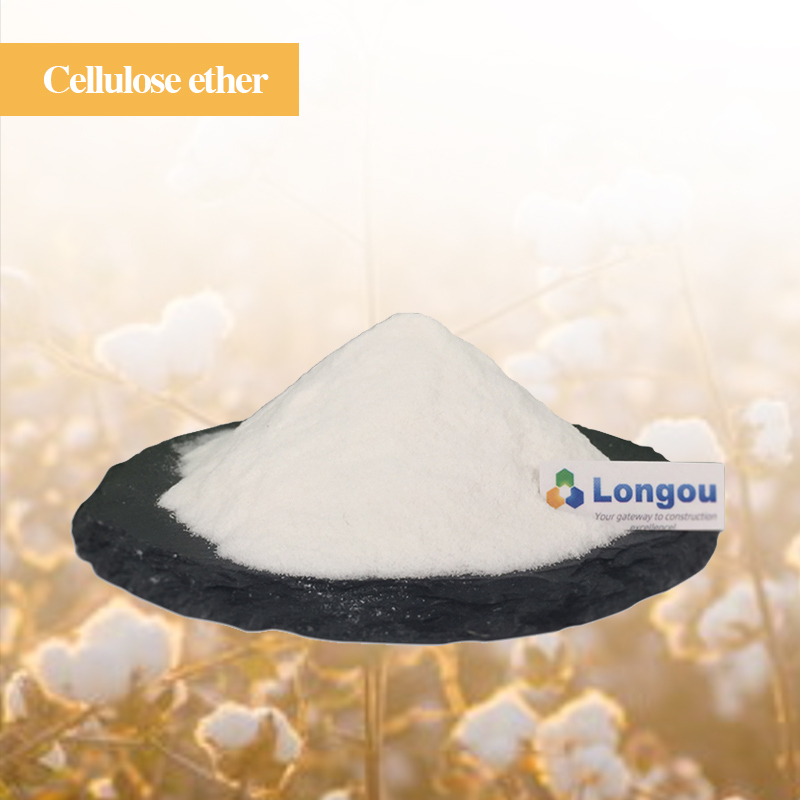
Technical Specification
Name |
|
CAS NO. |
9004-65-3 |
HS CODE |
|
Appearance |
White powder |
Bulk density(g/cm3) |
19.0--38(0.5-0.7) (lb/ft 3) (g/cm 3 ) |
Methyl content |
19.0--24.0(%) |
Hydroxypropyl content |
4.0--12.0(%) |
Gelling temperature |
70--90(℃) |
Moisture content |
≤5.0(%) |
PH value |
5.0--9.0 |
Residue (Ash) |
≤5.0(%) |
Viscosity ( 2% Solution) |
500(mPa.s, Brookfield 20rpm 20℃, -10%,+20%) |
Package |
25(kg/bag) |
Applications
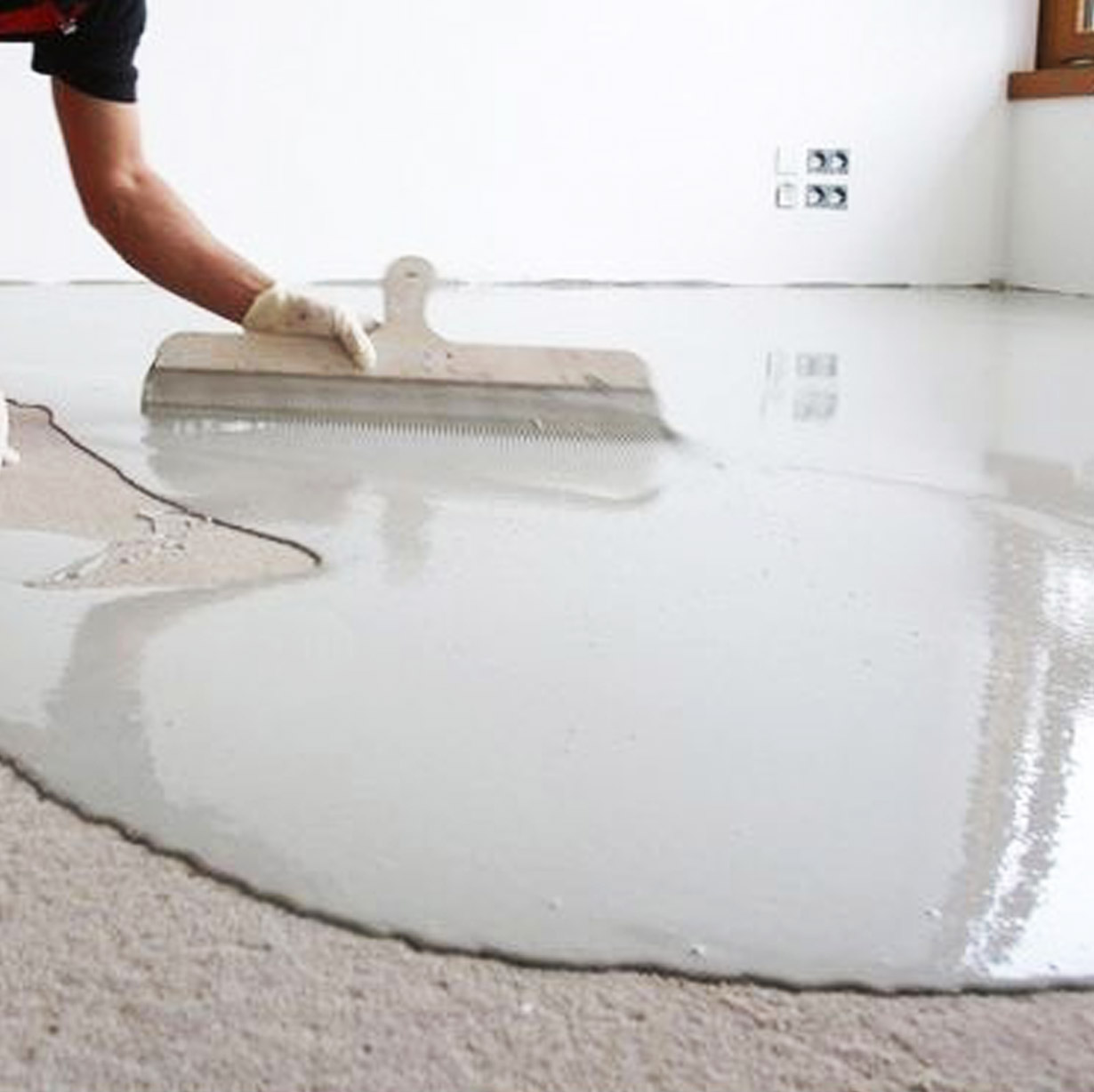
Main Performances
➢ Little impact on liquidity
➢ Excellent water retention effect
➢ Excellent Suspension Performance
➢ Little effect on the hardened surface
☑ Storage and delivery
It should be stored and delivered under dry and clean conditions in its original package form and away from heat. After the package is opened for production, tight re-sealing must be taken to avoid ingress of moisture.
Package: 25kg/bag, multi-layer paper plastic composite bag with square bottom valve opening, with inner layer polyethylene film bag.
☑ Shelf life
The warranty period is two years. Use it as early as possible under high temperature and humidity, so as not to increase the probability of caking.
☑ Product safety
Hydroxypropyl methyl cellulose HPMC LK10M does not belong to hazardous material. Further information on safety aspects is given in Material Safety Data Sheet.
FAQS
Hydroxypropyl methylcellulose (HPMC) are cellulose ethers that have had hydroxyl groups on the cellulose chain substituted for a methoxy or hydroxypropyl group. It is made by special etherification of highly pure cotton cellulose under alkaline conditions. In recent years, HPMC, as a functional admixture, mainly plays roles in water retention and thickening in the construction industry and is widely used in drymix mortars, like tile adhesive, grouts, plastering, wall putty, self leveling, insulation mortar and etc.
Normally, for putty powder, the viscosity of HPMC is enough at about 70,000 to 80,000. The main focus is on its water retention performance, while the thickening effect is relatively minor. For mortar, the requirements for HPMC are higher, and the viscosity needs to be around 150,000, which can ensure that it works better in cement mortar. Of course, in putty powder, as long as the water retention performance of HPMC is good, even if the viscosity is low (70,000 to 80,000), it is acceptable. However, in cement mortar, it is more ideal to choose HPMC with a larger viscosity (more than 100,000), because its water retention effect is more significant in this situation.
The problem of putty powder removal mainly depends on the quality of calcium hydroxide and has little to do with HPMC. If the calcium content of calcium hydroxide is low or the ratio of CaO and Ca(OH)2 is inappropriate, it may cause the putty powder to fall off. Regarding the impact of HPMC, it is mainly reflected in its water retention performance. If the water retention performance of HPMC is poor, it may also have a certain impact on the depowdering of putty powder.
The requirements for the use of putty powder are relatively low. A viscosity of 100,000 is enough. The key is to have good water retention properties. In terms of mortar, the requirements are relatively high and higher viscosity is required, and the 150,000 product has better effect.